The automotive industry is undergoing its biggest technology shift since the adoption of internal combustion, which makes training new designers, engineers and service technicians absolutely crucial. Arguably, this is nowhere more apparent than the aftermarket, where the current generation of petrol, diesel, hybrid and electric cars will soon require complex maintenance and parts support. To meet the future repair needs of motorists, apprenticeship and training programmes at aftermarket manufacturers and garages must be firing on all cylinders.
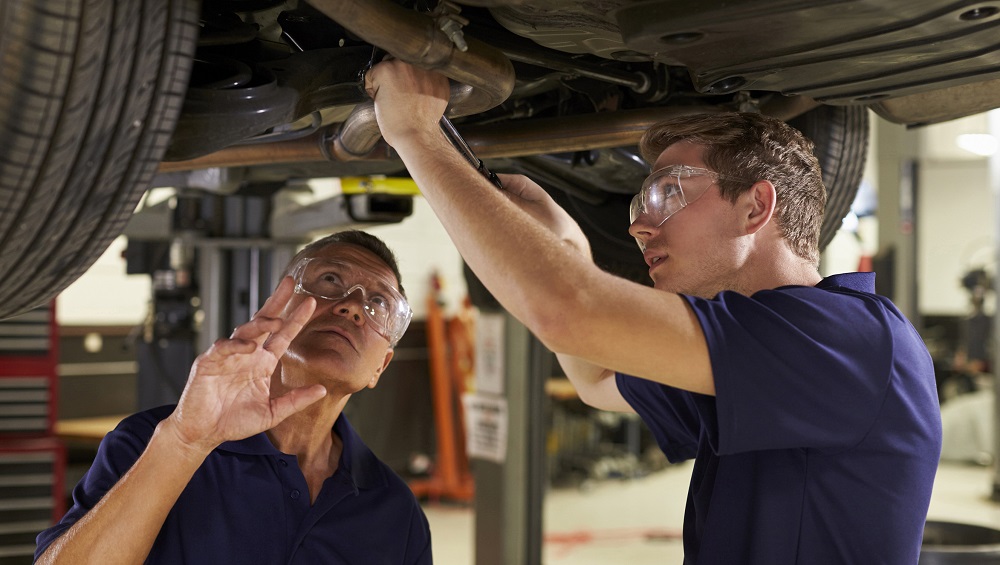
Making the grade for the UK car parc
Quantifying an automotive ecosystem that features an unrivalled diversity of powertrains and driver assistance technologies might be the premier challenge for the industry – but training isn’t far behind. This was recently illustrated by the Institute of the Motor Industry (IMI) which showed that overall automotive certifications decreased 5% in Q4 2023, while automotive apprenticeship starts dropped by 6% in the first half of the 2023/2024 academic year compared to the previous year (1).
While attracting new talent is essential for original equipment manufacturers (OEMs) looking to achieve the next breakthrough, the impact of a skills gap in the aftermarket would be more keenly felt by motorists. The total UK car parc has grown to around 36 million, constituting everything from old classics to electric vehicles (2). All these cars require regular maintenance and spare parts to stay roadworthy. Without training new staff and growing their skills, both service garages and aftermarket manufacturers could struggle to properly support such a large, diverse car parc – let alone the latest technologically advanced models.
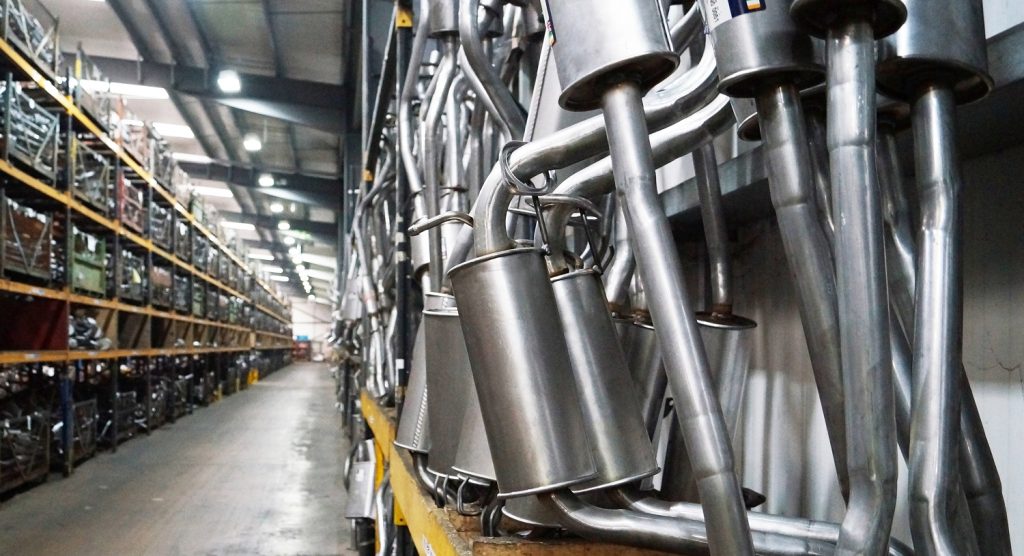
A part of the problem
While many will have experienced booking far in advance at the garage, the aftermarket parts supply chain isn’t as readily visible unless you’re an enthusiast running a rarer car. Speed of repair not only relies on garage expertise and capacity, but the ability to access quality aftermarket parts from reputable manufacturers. The nature of the UK car parc means a high quantity and variance of products is required. Any bottleneck in the development, manufacture or delivery of these parts reduces availability, increasing repair times and forcing motorists towards more expensive or unsuitable alternatives.
Take exhausts for example. Years of tightening Euro standards and widespread electrification has resulted in a profusion of different OEM exhaust designs with diesel particulate filters (DPFs), select catalytic reduction (SCR) and petrol particulate filters (PPFs). To support motorists, aftermarket exhaust manufacturers have had to adapt fast, researching, developing, testing, introducing and delivering a wide range of OEM equivalent replacement systems. Successfully maintaining this pace longer term relies on growing capacity across businesses by attracting and nurturing new talent.
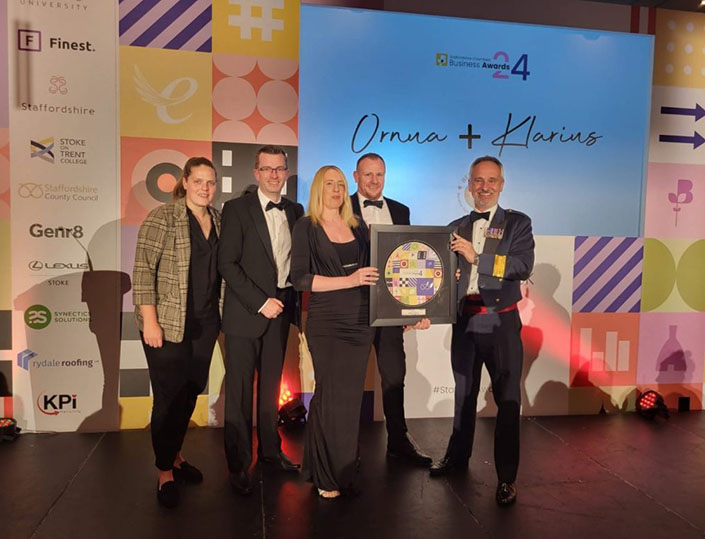
Top of the class in the aftermarket
Staffordshire-based Klarius Products is the largest UK manufacturer of aftermarket exhausts and has built a successful apprenticeship programme so it can meet multiple industry challenges.
Sarah Ratchford, Head of HR at the Klarius, explains: “Our employee strategy is not just a priority, it is a fundamental aspect of who we are as an organisation. Through our comprehensive approach to recruitment, training and support, we aim to create clear pathways for career progression, empowering our employees to reach their full potential.
“We take immense pride in our commitment to apprenticeships, 4.5% of our workforce are foundational level apprentices, which is 1 percentage point above the national average, and we have a further 1.3% pursuing degree level apprenticeships. This ensures that we have a mix of dynamism, experience and capacity in our team, helping us to deliver more quality products to our customers.”
Eyes on the road to success
The policy is more than just words. Klarius’ latest Quality Engineer, Kieran Rowe, began in the warehouse before completing his Quality Apprenticeship and switching role. With the increased technicality of modern exhausts for petrol, diesel and hybrid vehicles, Kieran will help ensure Klarius products meet the required standard.
Training opportunities are available across the business. Sarah, herself, is undertaking a Level 7 Senior Leadership Apprenticeship through Axia Solutions – a course exclusively for women. Fostering a cohesive and supportive working environment will keep talent within the business.
With the aftermarket facing more challenges than ever before, new skills must be developed, and service capacity found. Effectively meeting the repair needs of motorists while responding to a sector in flux requires long-term thinking with regards to infrastructure, technology, development and staff. By investing in training and apprenticeships, aftermarket manufacturers can take a large step towards whichever direction the automotive industry decides to take.
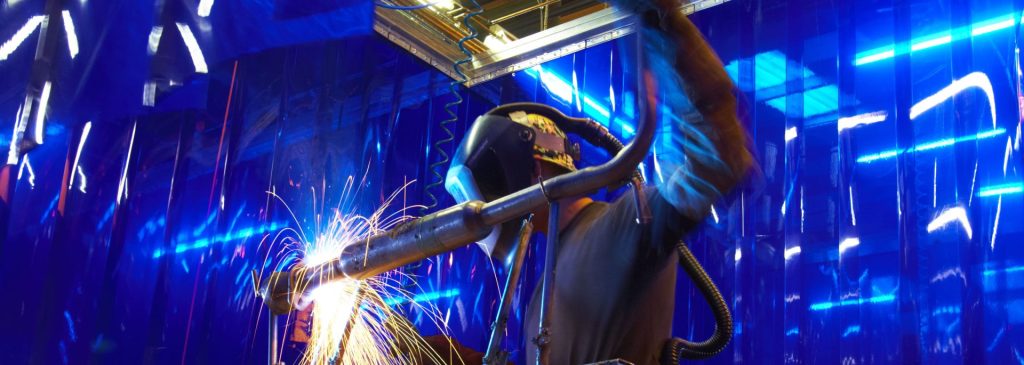